こんにちはSHIMONです
世界一かっこいいカゴをデザインし販売をしています
SONYで働いていたMさんを紹介され、とうとう自分の理想のカゴを作るという夢が10年以上経て現実になろうとしていました。
SONYという会社は、個々人の独立起業を支援する取り組みも行っており、Mさんも独立起業を目指しているとのことでした。今回のスモールサイズのプロダクトに関わった経験もあるらしく、まずは相談に乗ってもらうことになりました。
紹介を受けたMさんを訪ねるために、品川にあるSONYの本社に行くことになりました。仙台の地方都市に住んでいる私にとって、大都会の品川にある会社は目が回るような別世界のように感じました。
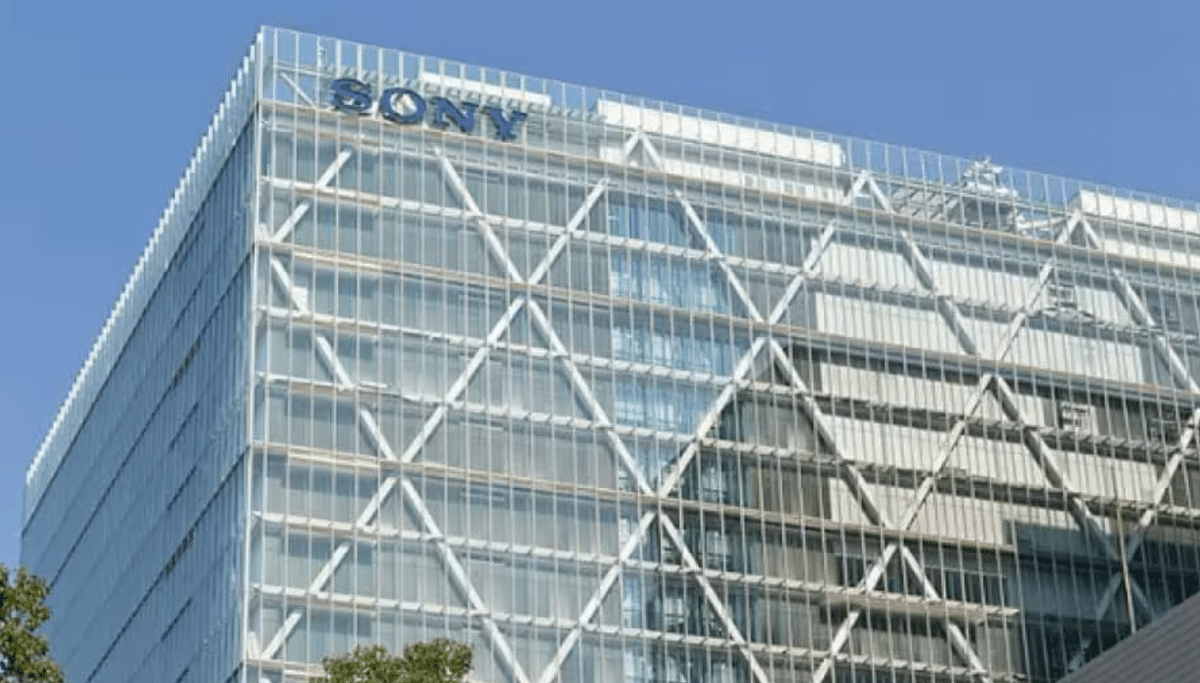
大会社に似つかわしくないラフな服装のMさんが迎えてくれました。紹介してくれたHさんは、私がカゴを作りたいということを軽く伝えておいてくれましたが、Mさんはカゴを作るということに全く理解が及んでいない様子でした。そこで私は、自分のカゴに対する熱い思いと今までに考えていたアイデアを伝えました。すると、彼はプロダクト製品の製品化に至るまでの流れを教えてくれました。
右も左もわからない私にとって、T1やT2といった聞き慣れない語句が並びました。
プロダクトの製品化プロセスにおける「T1」や「T2」という用語は、通常、製品開発の特定の段階を指します。これらの段階は、開発プロジェクトの進行を追跡し、評価するために使われます
T1(Technology Readiness Level 1)
-
概念の証明段階:基本的な原理や技術の概念が証明される段階。初期の研究開発段階で、アイデアが実際に動作するかどうかを確認します。
T2(Technology Readiness Level 2)
-
技術概念とアプリケーションの定義:T1で確認された概念を基に、具体的な技術や応用の可能性を評価する段階。ここでは、基本的な技術や理論がどのように実現可能かを検討します。
T3(Technology Readiness Level 3)
-
実験的証明:初期の実験を通じて技術の実現可能性をさらに証明する段階。プロトタイプやモデルが作成され、実験室レベルでのテストが行われます。
これらの段階は、プロジェクトが進行するにつれて、より詳細な評価やテストが行われ、製品化に向けて技術の成熟度が高まっていくことを示します。
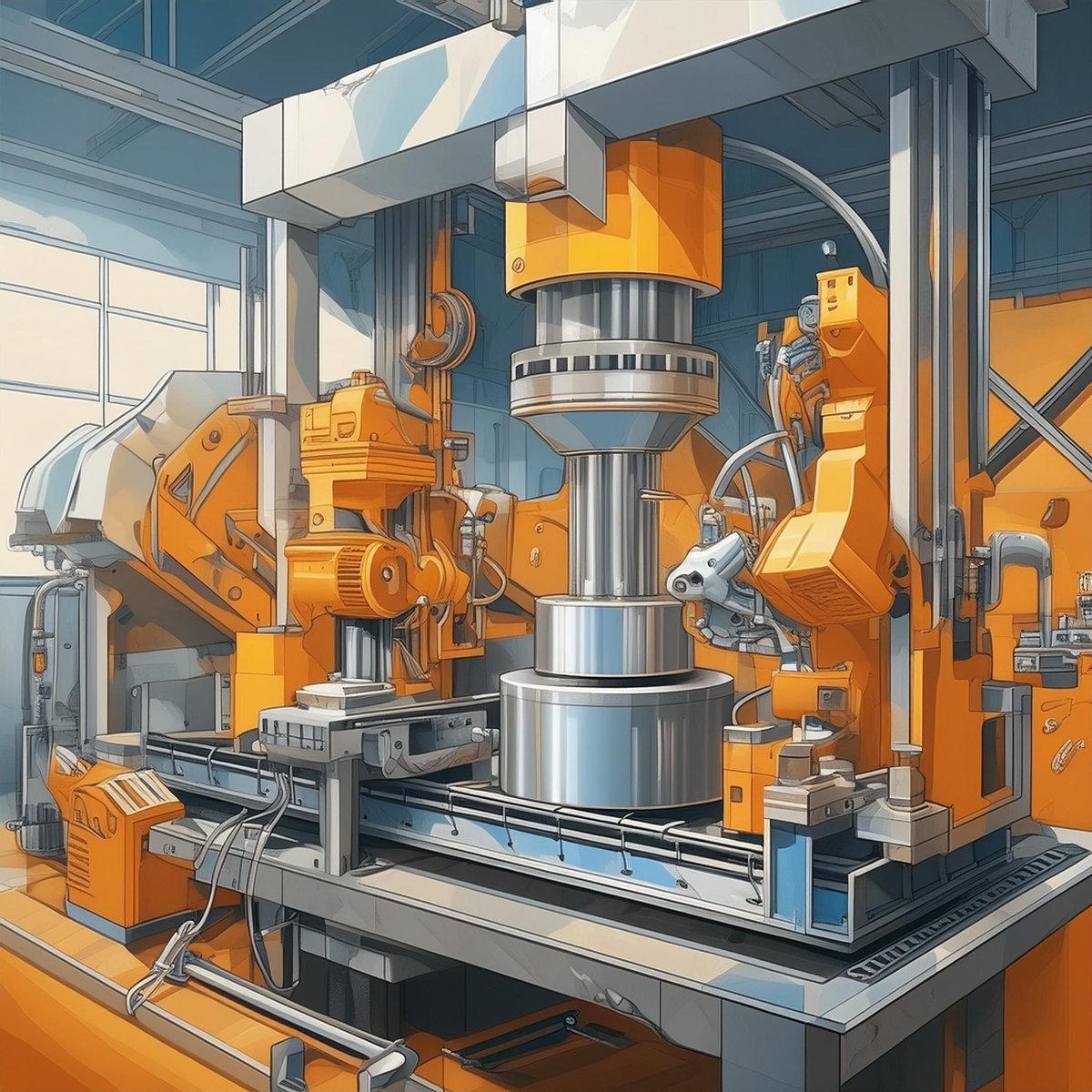
まずはカゴを作るにあたってどの様な作り方をするかが問題になりました。
MさんはSONYのテレビを作っており、テレビの裏面のプラスチックカバーは通常、射出成形(インジェクションモールド)という製造方法で作られています。射出成形は、溶かしたプラスチックを金型に射出し、冷却して成形するプロセスです。この方法は以下のような特徴を持っています:
-
大量生産に適している:射出成形は、一度に多くの製品を効率的に作ることができるため、コスト効率が高いです。
-
高精度:複雑な形状や細かいディテールも高精度で再現することができます。
-
素材の選択肢が広い:さまざまな種類のプラスチック材料が使用できるため、製品の性能や外観に応じて最適な素材を選ぶことができます。
-
仕上がりが良い:成形後の製品は滑らかで、追加の加工が少なくて済む場合が多いです。
テレビの裏面カバーは、耐久性、軽量性、コストパフォーマンスが求められるため、射出成形によって作られることが一般的です。この作り方意外にも
熱成形(Thermoforming)
熱成形は、プラスチックシートを加熱して柔らかくし、型に押し付けて成形する方法です。以下がその手順です:
-
加熱:プラスチックシートを所定の温度まで加熱し、柔軟にします。
-
成形:加熱されたプラスチックシートを型に押し付けます。このとき、真空や圧力を使ってシートを型に密着させます。
-
冷却:成形されたプラスチックを冷却し、形状を固定します。
-
仕上げ:不要な部分を切り取って、製品を仕上げます。
真空成形(Vacuum Forming)
真空成形は熱成形の一種で、真空を使ってプラスチックシートを型に密着させる方法です。以下がその手順です:
-
加熱:プラスチックシートを所定の温度まで加熱します。
-
成形:加熱されたプラスチックシートを型にかぶせ、真空ポンプを使って空気を抜き、シートを型に密着させます。
-
冷却:成形されたプラスチックを冷却し、形状を固定します。
-
仕上げ:不要な部分を切り取り、製品を仕上げます。
曲げ加工(Bending)
特定の部分を曲げる方法もあります。この方法では、局所的にプラスチックを加熱して曲げたい部分だけを柔らかくします。以下がその手順です:
-
加熱:曲げたい部分を局所的に加熱します。加熱装置や熱風機を使って特定の範囲だけを柔らかくします。
-
曲げ:加熱された部分を希望の角度に曲げます。専用の治具や手作業で曲げることが一般的です。
-
冷却:曲げた部分を冷却し、形状を固定します。
話し合いの結果、カゴの形状や大量生産の方法を考慮して、射出成形を選ぶことになりました。カゴの形状は定型が決まっており、特にかっこいいカゴを作るのは簡単だろうと思っていましたが、ここからが苦労の連続でした。次回からは、その苦労やブランドのデザイン部分についてお話ししたいと思います。